Machine-integrated solutions
The right solution for every machine. Ask our experts.
Our machines offer different methods for workpiece removal – quickly, safely, and gently.
- Removal or flushing out by counter spindle or turret.
- Gantry system for discharging workpieces onto a belt by means of grippers.
- Flexible feed and discharge with single or double gripper. Expandable with bath systems, robots, palletizing stations.
- Machine-integrated robot solution for multi-spindle machines
Gantry-type removal unit with conveyor belt (e.g., WH1, WH2)
Applications
- Z axis gantry-type removal unit with NC drive
- Automatic removal of the finished workpiece from the main or counter spindle, which is then placed onto a conveyor belt or into a workpiece container.
- Removal of the remnant from the main spindle in the case of bar stock machining, which is then placed into a remnant container.
The gantry-type removal unit is composed of the following components:
1. Position-controlled numerical Z8 axis
An electric motor drives the gripper arm via a belt and gearbox. The measuring system is in the motor. It is possible to move to any position.
2. Gripper swivel movement
To move around the counter spindle, the gripper must be swiveled out or in. This motion is achieved pneumatically between two end stops.
3. Workpiece gripper
The workpiece or the bar remnant is picked up at the spindle center by gripper jaws operated on both sides.
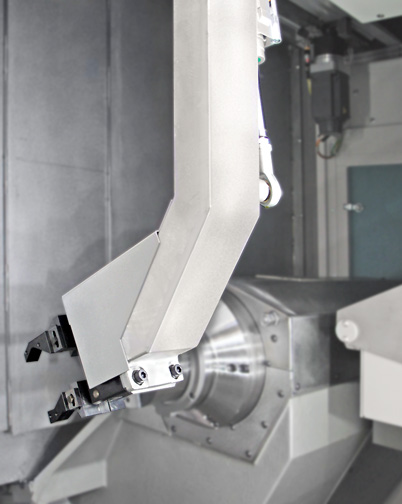
Workpiece handling (e.g., WHU)
The integrated workpiece handling unit is available as an option. It can be used for loading and unloading as well as for the removal of remnants and is suitable for parts weighing up to 25 kg and with a diameter of up to D 120 mm. The handling unit is equipped with 2 CNC axes that are operated from the machine control.
Further individual automation solutions, such as conveyor belts or robot handling with ancillary functions, can be integrated on a customer-specific basis.
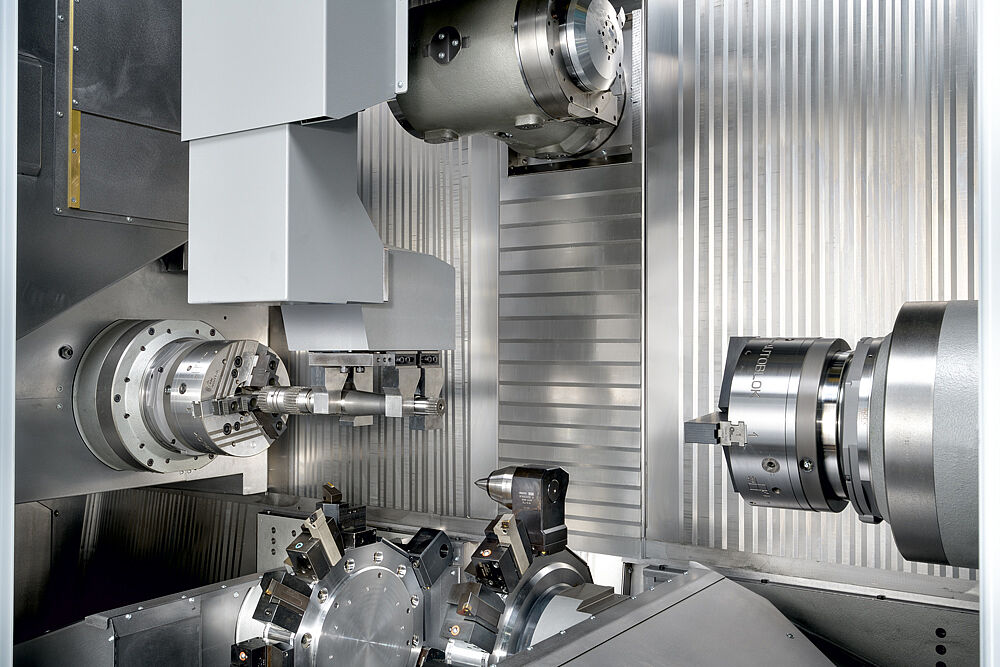
Machine-integrated solutions for multi-spindle machines
Stationary workpiece removal
(part removal via internal chute and conveyor belt)
The workpieces fall onto the internal conveyor belt through a chute and are then deflected 90° by a second chute to reach an external conveyor belt
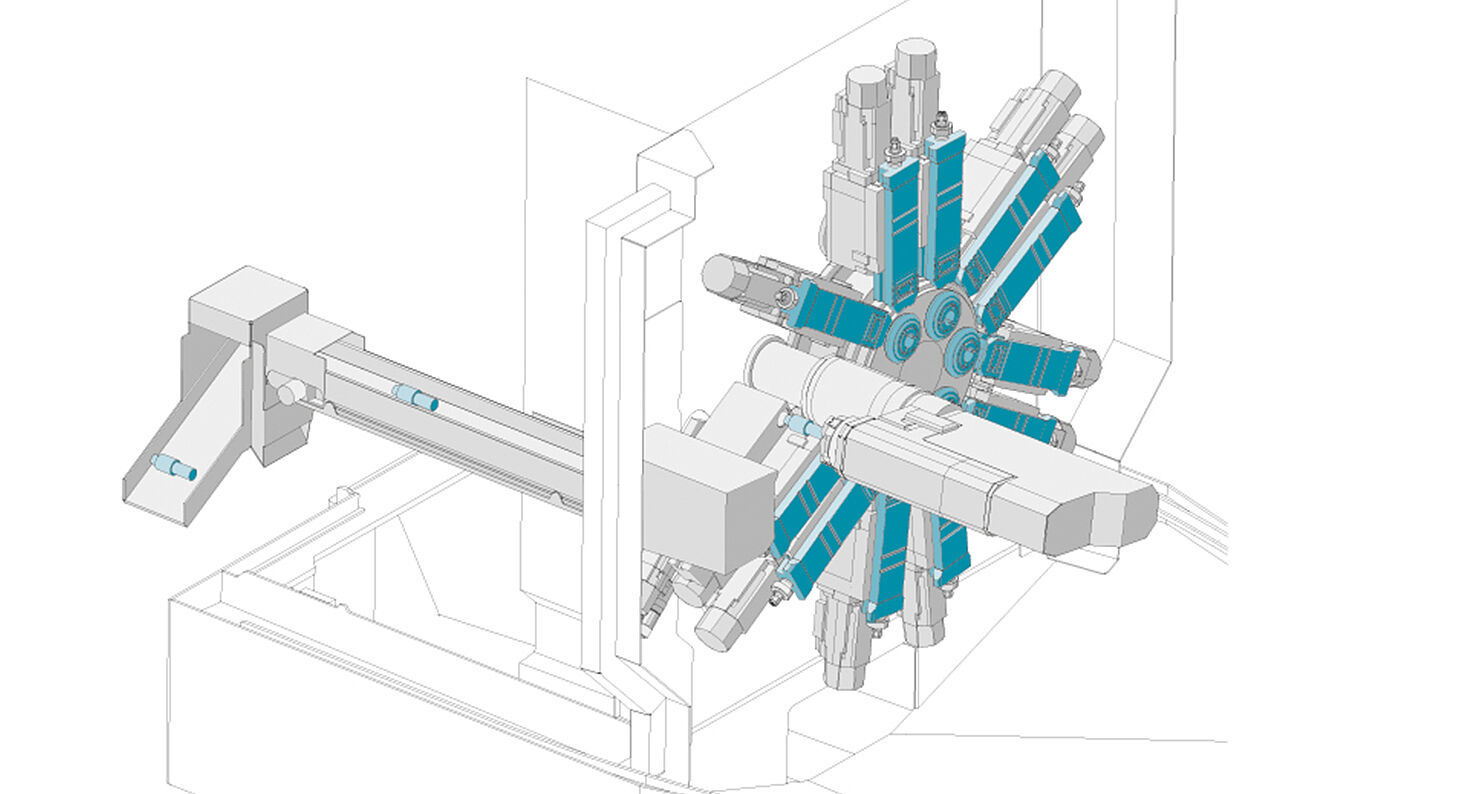
Position-aligned workpiece removal with integral parts conveyor
Workpieces are removed from position 6 by the synchronous spindle and are position-aligned to the internal conveyor belt for parts that are not to be ejected.
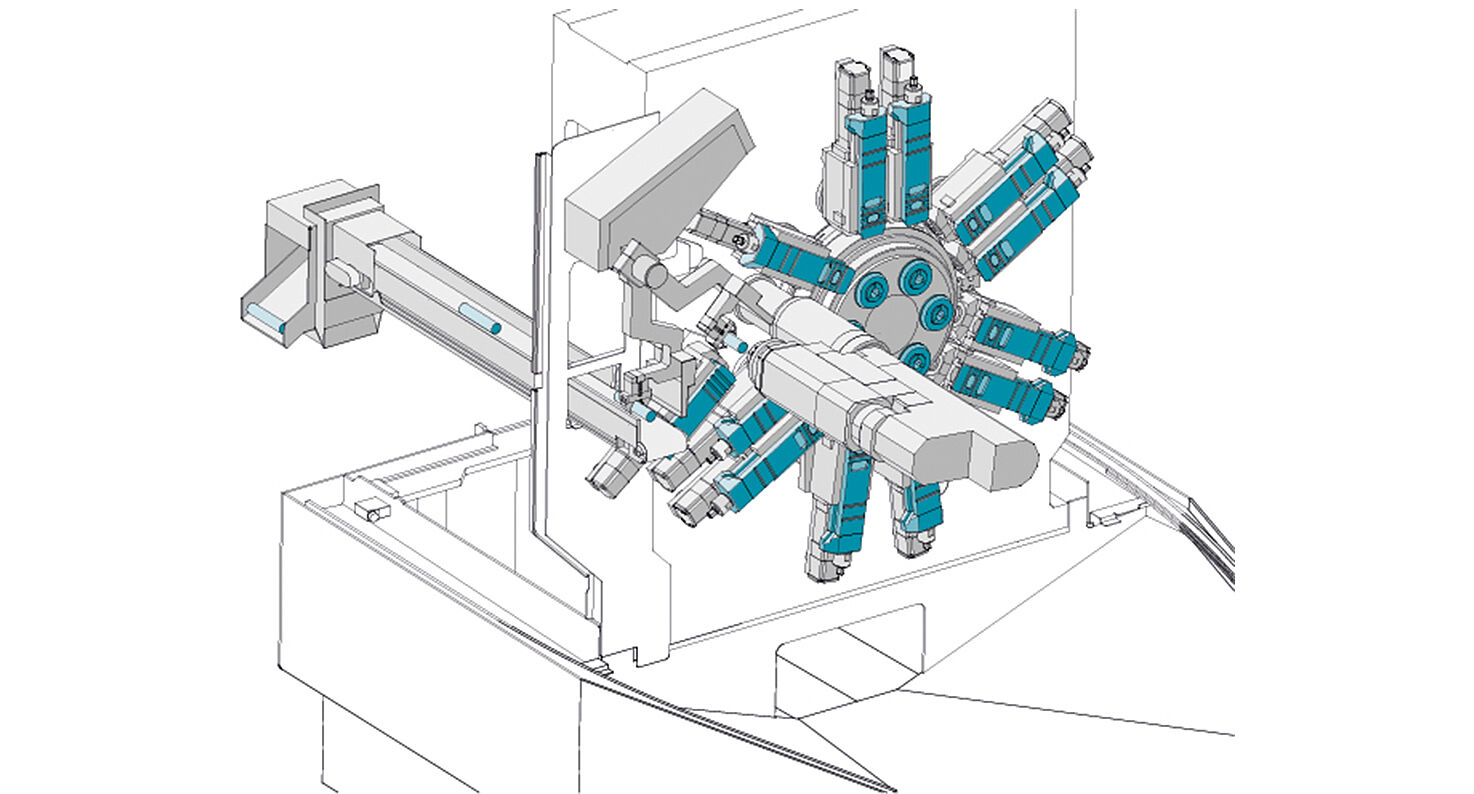
Position-aligned workpiece removal with intermediate gripper and linear shuttle
Rapid, damage-free, position-oriented removal by a linear and rotary motion. The workpieces are transferred first from the synchronous spindle to the intermediate gripper. Then the linear shuttle transfers the workpieces to the external handling system.
This procedure takes place during secondary processing time.
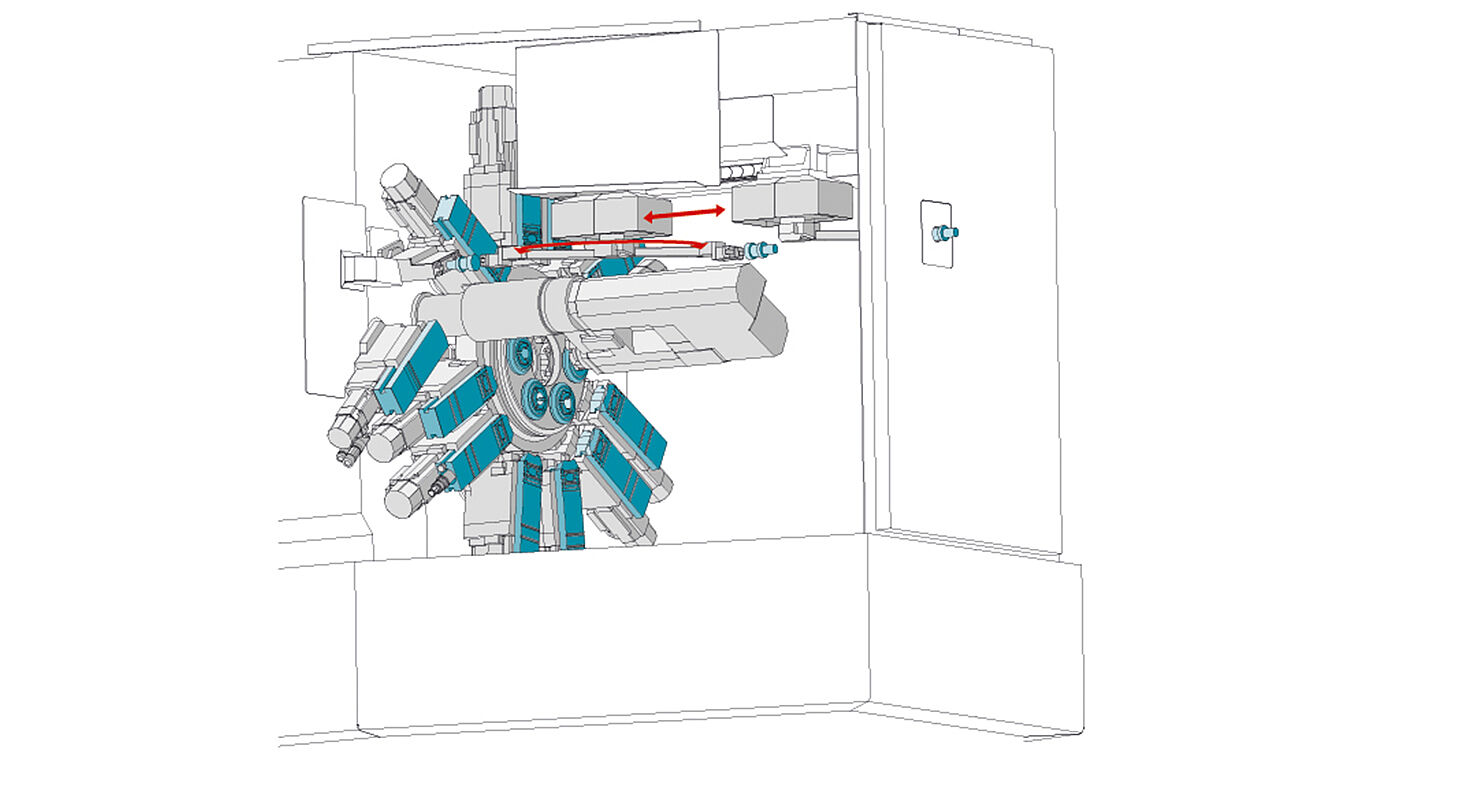
Parts feed and removal by a 6-axis robot via the swivel disk to the external handling system
The workpiece handling system for chuck parts and bar segments can be used for 6-spindle machining with and without synchronous spindle, and also for double 3-spindle machining. A 3 x OP10 (first side) and 3 x OP20 (second side) variant, with external turning station, is also available.
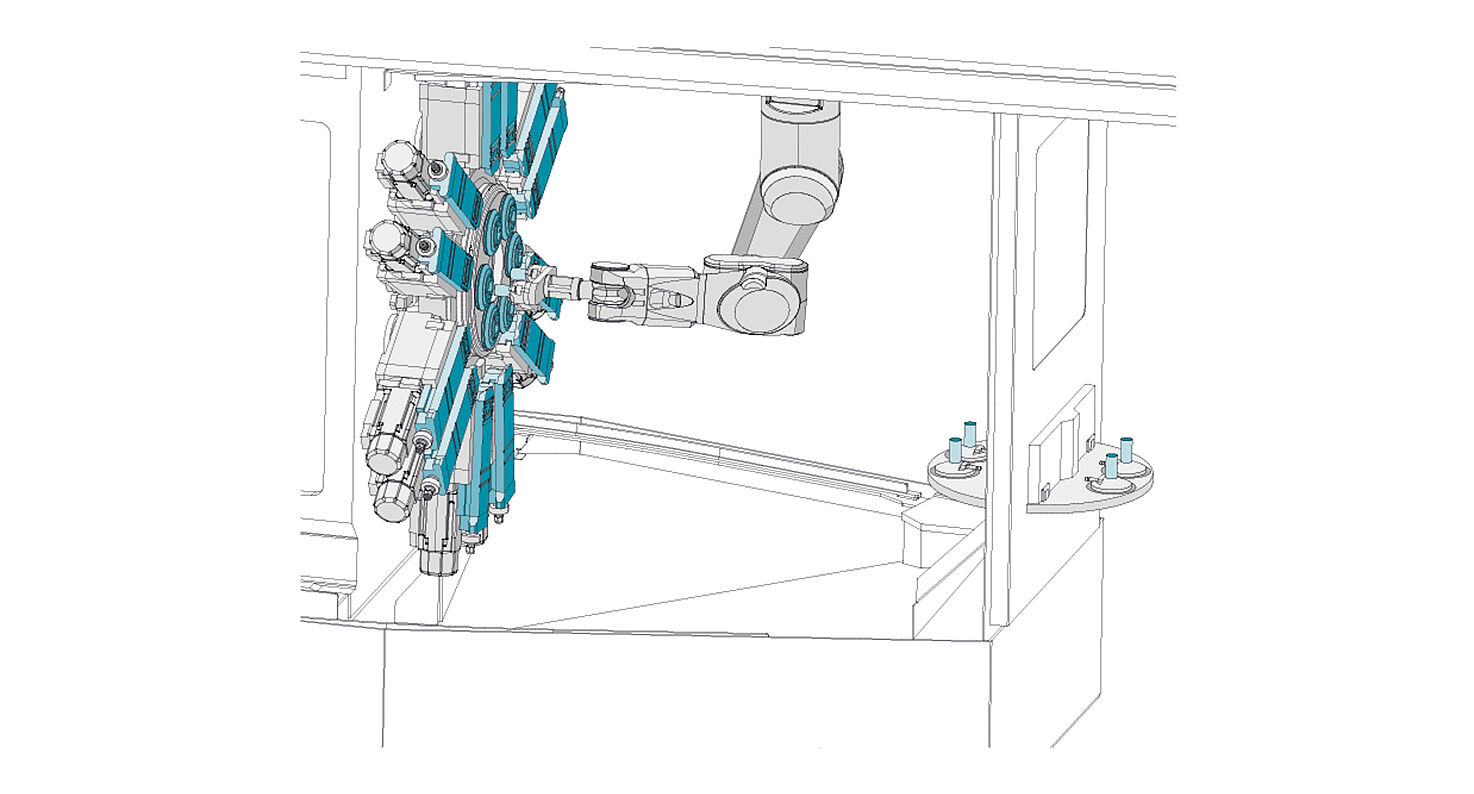