INDEX-grinding technology
Increase your productivity through process integration
Your benefits
Reduced cycle times
- Preturning instead of roughing
- Reducing the amount of grinding by preturning
- Plunge grinding along the entire workpiece length
Quality gain
- Surfaces in high and ultimate quality (Ra < 0.1 µm)
- Twist-free surfaces (e.g. For sealing ring seats)
- Process monitoring by in-/post-process measurement
Increased process reliability
- Process-reliable keeping of extremely small tolerances
- Very good automation by regular dressing (tool wear during turning)
- Process tracking by in-/post-process measurement
WE NEED YOUR CONSENT!
This content is provided by Youtube.
If you activate the content, personal data may be processed and cookies set.
Accept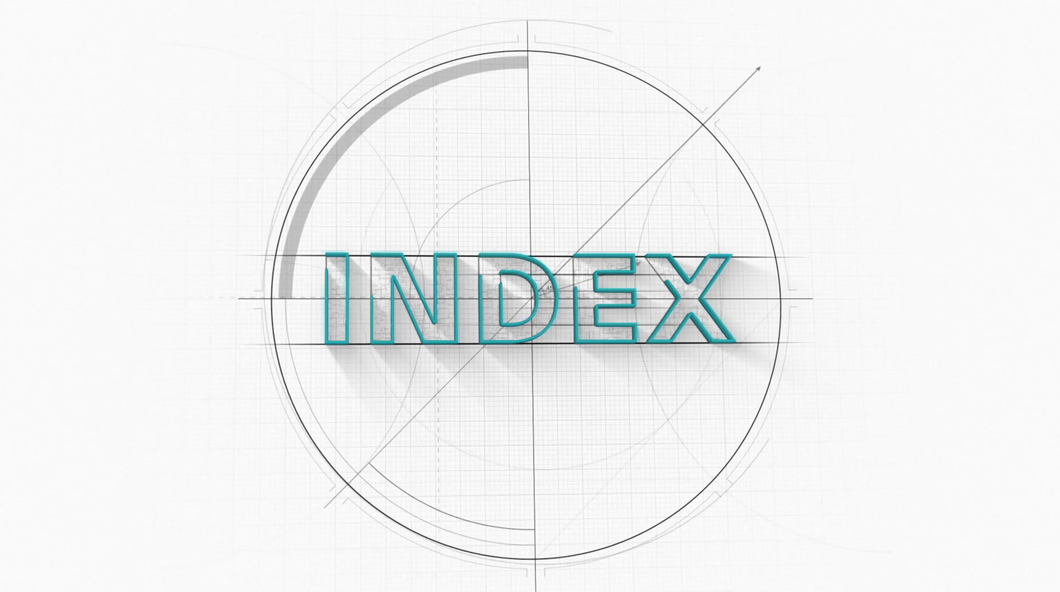
External grinding spindle
You will not miss your grinding machine: Due to the large-dimensioned high-precision rolling bearings, you’ll achieve maximum rigidity and precision. Of course, conventional, CBN and diamond tools can be used on INDEX turn-grind centers.

Grinding tool holders
The use of INDEX grinding tool holders provides optimal conditions for reliable complete machining of your workpieces. This reduces throughput times and you do not need a grinding machine. And not only that – to increase efficiency, many grinding cycles for OD, face, slot and flat grinding are already included in the control upon delivery of the machine.
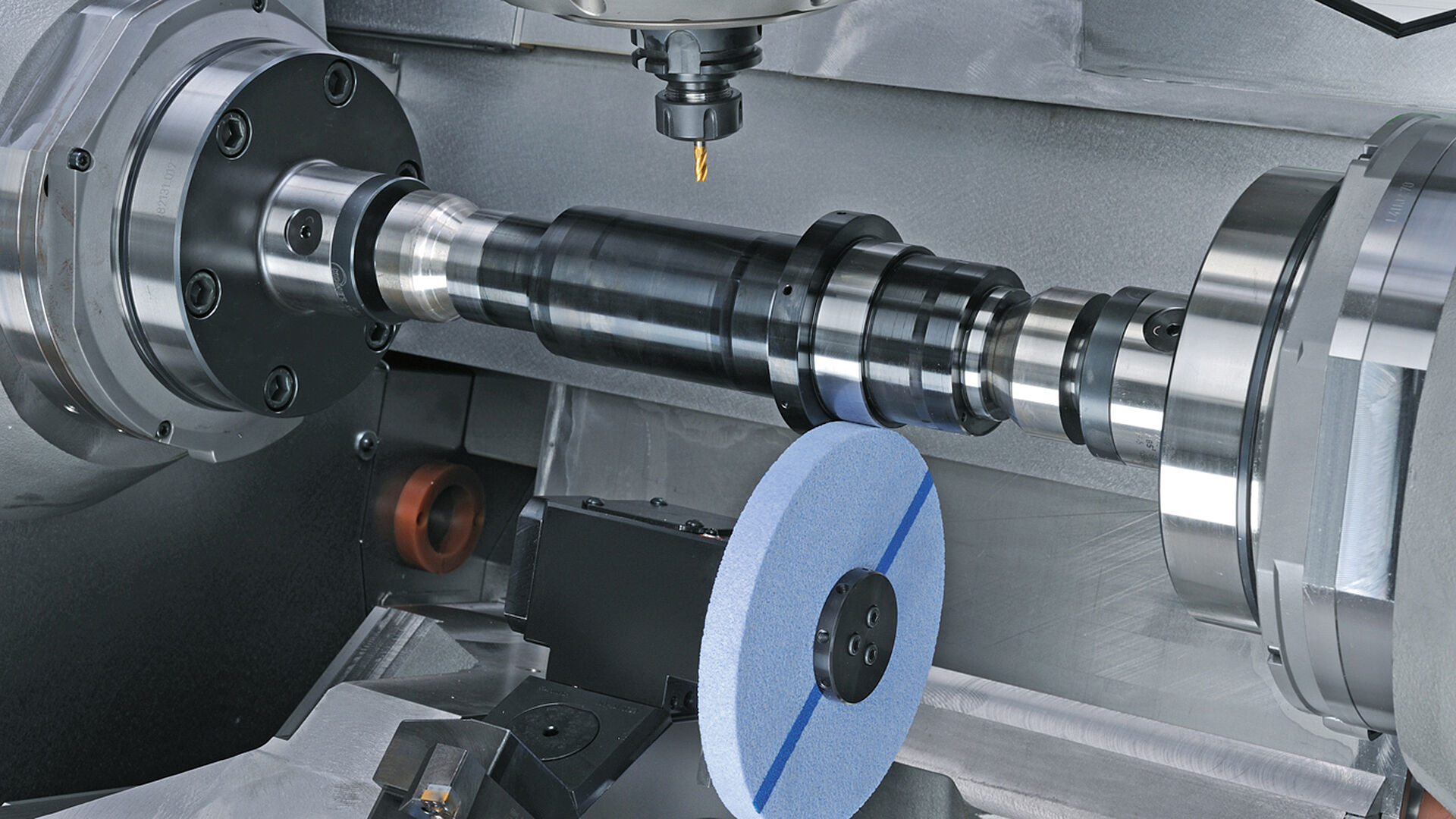
Grinding with motorized milling spindle
Take advantage of the groundbreaking possibilities for internal, external and flat grinding. The unique kinematics allows you simultaneous grinding on the front and back in 5 degrees of freedom. Due to the high tool pool in the magazine (up to 152 locations on the INDEX R300), you’ll save setup times and always have the right tool at hand.
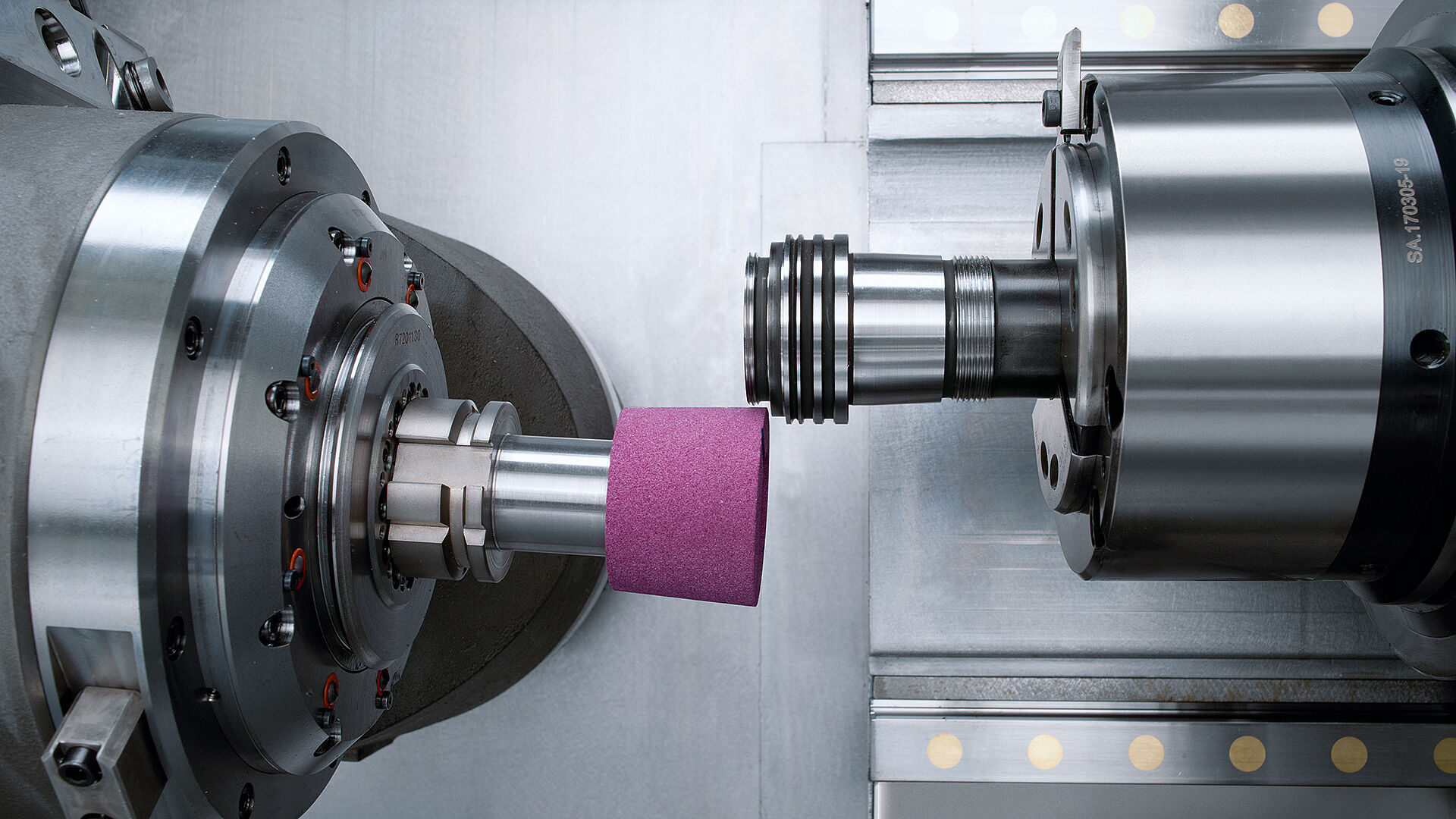