TRAUB TNL20 - a very high-performance automatic turning machine
Productive sliding and fixed headstock turning of medium and high complexity workpieces from bar stock or with an integrated robot cell
Machine highlights TNL20
Your benefits
- Simultaneous machining with 2, 3 or 4 tools
- High tool pool for set-up-friendly production
- Short tool changing times by means of CNC indexing axis in the tool turrets and in the front working attachment
- Generous and process-reliable work area
- Intelligent automation through the integrated robot cell iXcenter
Machine concept
The machine concept of the TNL20 has been systematically matched to the daily requirements of the user. So the kinematics of the machine allows effective and simultaneous machining with two or three tools.The generous and vertically arranged work area provides for the necessary degrees of freedom, as well as for very high process reliability. The machine's crucial productivity advantage is the result of its extraordinarily high dynamics. The newly developed machine bed from gray cast iron forms the basis for utmost vibration dampening properties. And the high rigidity and thermal stability ensure optimum workpiece quality.
TNL20 in focus
Robot cell iXcenter
Intelligent automation - even more flexibility and efficiency
With the optional robotic cell, blanks and/or finished parts can be supplied and discharged quickly, safely and flexibly. The robot cell is integrated ergonomically into the machine. It can be moved easily to the left during the setup process, allowing unobstructed access to the work area of the machine. During production, the robot cell is fixed in front of the machine's work area. The robot then accesses the work area via the sliding guard of the machine, which opens automatically behind the robot cell.
Space-saving handling of blanks and finished parts
- Space-saving vertical storage with up to 14 pallets stacked up
- Pallets with blanks are loaded at the top, pallets with finished parts are removed at the bottom
- The pallet is pulled out by the robot
- The pallet storage cycles down in steps of 25.4 mm
- Easy macro-programming
Using more potentials
The space above the vertical storage can be used easily for subsequent processes such as cleaning, measuring, deburring, etc. The preparation for incorporating a fully automatic 3D measuring cell is already provided as standard
- Closed-loop process control is possible
- SPC parts output and NOK parts output is provided
Video TNL20
Machining of a medical screw
WE NEED YOUR CONSENT!
This content is provided by Youtube.
If you activate the content, personal data may be processed and cookies set.
Accept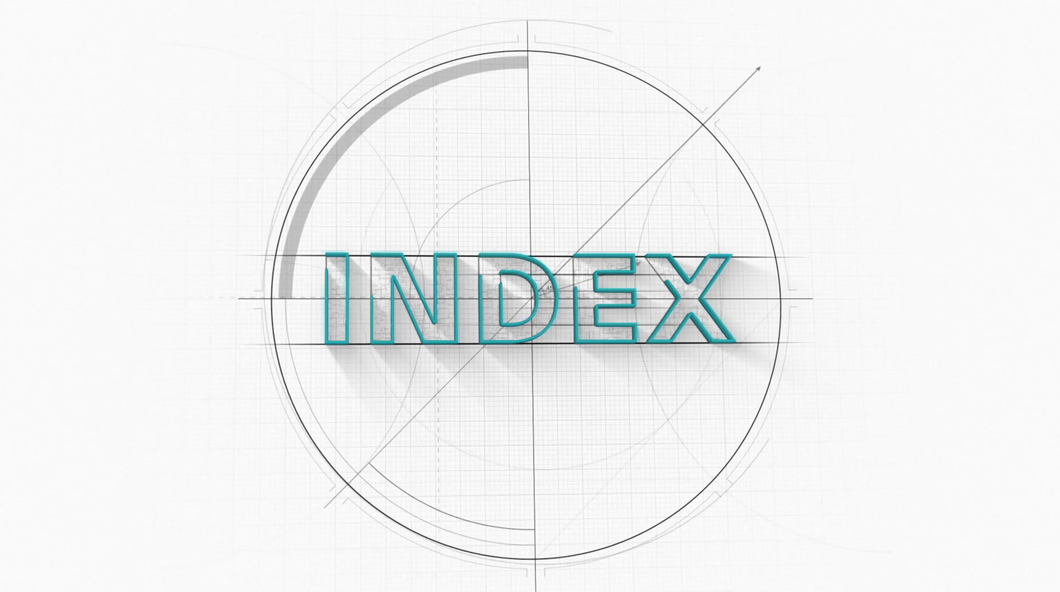